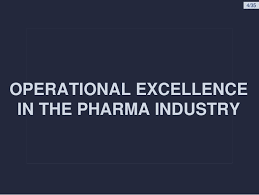
05
Jun
Operations Excellence Impact in Pharma companies
Operational excellence (OE) is the overarching mindset and approach that enables an organization and it people to sustain development over time.
OE is a philosophy and mindset in business that positions its strategies and people around problem-solving and leadership. It helps to ensure that processes are designed to prioritize the customer's needs, while also supporting the morale of internal stakeholders like employees. As such, employees feel motivated and inspired to deliver results to the best of their abilities.
With OE, employees also have the training, resources and most importantly, the positive mindset to act as constructive, analytical thinkers and problem-solvers. This means that if and when an issue arises, they have the confidence and knowledge to address and resolve it. Overall, having an attitude geared towards operational excellence becomes part of the company culture. This helps to serve the inner workings of business better, and ultimately, its customers.
When operational excellence exists within a business, the business is positioned to beat out the competition because it can perform more reliably and strategically by lowering costs, lessening risk and ultimately, increasing revenue.
There are specific methodologies, but from a top-line view, here are three critical elements:
- Develop an integrated working environment with a seamless flow (a fundamental way to make this happen is to leverage proven concepts, technology and automation software to your advantage)
- Create a culture that prioritizes Operational Discipline, or doing the right thing, every time
- Build a team that believes in supporting one another and delivering value to the customer
Following are some of the Pharma industry specific success stories, companies that took up the Operational Excellence journey and achieved the targeted milestones (impact).
Case 1:-
Debottlenecking project in a Pharma company saw the real benefit, EUR 2.6 million.
The situation at the start
A mid-sized pharmaceutical company which produces API anticipated increasing demand for one of the most strategic APIs produced in their Italian plant.
The company took up the Operational excellence journey to find out the most convenient technological and organizational solution to manage the increase in volume from the plant.
Putting strategy into action
A cross-functional team was put in place to identify all the constraints that were limiting the volume of the plant. Analysis was done across technological, quality & regulatory (GMP), waste disposal and logistics domains to understand the bottlenecks/constraints and identify potential areas for improvements.
Based on constraints' analysis, different initiatives were identified for how current processes could be amended to allow greater production and the best CAPEX and OPEX solutions.
Deliver concrete results
A business case and implementation plan were defined for each initiative, along with the target implementation time and responsibilities assigned. The management decided to implement the best scenario initiatives and the real benefit that it generated of EUR 2.6 million.
Case 2: -
One of the Pharma player achieved 33% increase in overall throughput (for a major SKU manufacturing line) using Integrated Manufacturing Excellence Program that also helped them become more agile to address market requirements..
The situation at the start
The Company wanted to increase the capacity of sterile injectable with minimum Capex involvement and use of Operational Excellence tools to meet new demands for life-saving drugs during the COVID-19 pandemic and become agile to manage any sort of demand fluctuations.
Putting strategy into action
A cross-functional team was created. The team used Value Stream Mapping analysis (VSM), identified bottlenecks and defined potential for capacity improvement. Further, the team used six sigma problem-solving approaches to develop new ideas for overall capacity improvement keeping quality and regulatory (GMP) requirements in mind.
Deliver concrete results
- A sturdy plan was created with defined timelines for implementation and the PMO team was given a task to ensure smooth progress basis the defined milestones.
- As a result of identified initiatives, throughput improvement of 33% (changeover time reduction by 50%, increase in run time efficiency, reduced speed losses, breakdowns and other availability losses) was achieved during the critical COVID-19 pandemic period with an increase in revenue.
Case 3: -
In 2020, a Pharma major company reduced the average change over time in packaging lines from 8 hours to 1.5 hours. This was achieved through a collaborative Ops Excellence effort.
The situation at the start
The average time for an SKU (size) changeover on the packaging lines was taking approximately 8 hours. However, this type of performance was unsustainable as they wanted to grow the business at current growth forecasts.
Putting strategy into action
The OPEX team identified the need to reduce their equipment changeover cycle time with the introduction of lean manufacturing principles eg. SMED (Single Minute Exchange of Die) and TPM (Total Productive Maintenance).
Deliver concrete results
- The company adopted SMED as a site strategy in 2016 with dramatic results in the speed of changeovers. As a result, the business was able to be more flexible and agile with its production scheduling.
- The company introduced a Kaizen Card program. This encouraged employees to suggest items for continuous improvement.
- The Pharma company has dramatically reduced downtime across all lines. This was achieved by a combination of implementing Lean manufacturing concepts & training the operators to maintain their own equipment (Autonomous Maintenance). As a result, it reduced the overall changeover time and maintenance call-outs to repair lines and ultimately improved the Overall availability of Equipment.
Ps: all the above cases are extracted through open source information available on Google search engine.